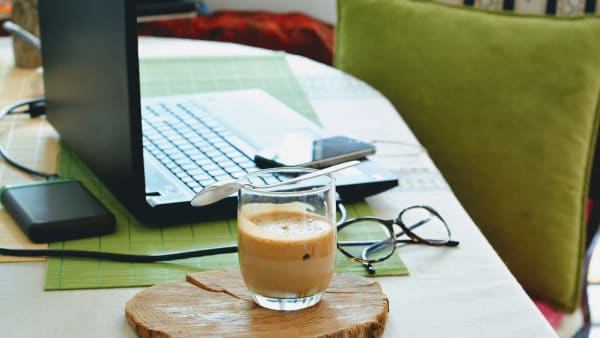
How To Hire A Quality Inspector
June 13, 2022
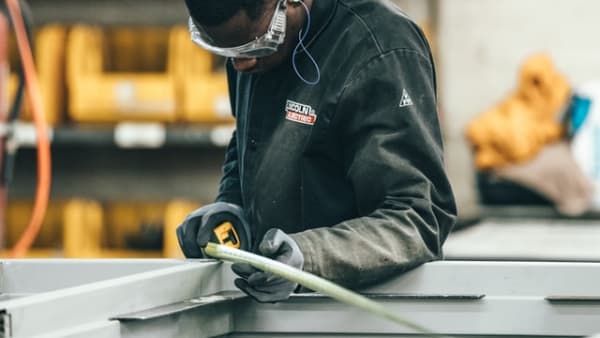
The work of a quality inspector is varied. Their work is focused on reviewing and monitoring a company's products or materials, ensuring they meet the necessary standards before going to market.
Quality inspectors work across many industries and sectors, from product manufacturing to food-related products. Working as part of a team, their role is central to an organization's reputation and the safety and quality of the product it manufactures. Their role also ensures that the specifications required by customers are adhered to, and that customer satisfaction is met at all times.
There are several skills and abilities needed to be an effective quality inspector, no matter the industry they are working in. This article explores these skills and technical abilities. The article also highlights the pre-employment tests that you can incorporate into your recruitment process, meaning that you hire the best candidates for the roles you have to fill.
What should a quality inspector be able to do?
The primary duty of a quality inspector is to ensure that the quality and standard of a product meet the necessary guidelines and customer requirements.
To do this, quality inspectors carry out routine monitoring, sampling, and analysis of source materials, in-process materials or products, and the finished product. They can work in various sectors, so they may be involved in calibrating or evaluating the effectiveness of machinery, or tasting the finished item should the product be food-related.
Quality inspectors analyze and interpret test results, comparing the results to safe parameters or agreed safety standards and reporting their findings should the results not be within agreed limits. In such cases, quality inspectors may be required to recommend solutions, report their findings to relevant authorities and stakeholders, or be involved in developing new testing methods.
The role of a quality inspector also involves investigating and resolving issues with machinery or materials, troubleshooting, or recommending follow-up actions.
Training new inspectors, liaising with other quality assurance team members and complying with regulatory requirements also form a crucial part of this role. Furthermore, quality inspectors are responsible for maintaining and updating standard operating procedures, ensuring the protocols are clear and relevant for each stage of the manufacturing process.
Skills to look for in a quality inspector
There are several skills commonly associated with successful quality inspectors. Assessing your candidate pool against these skills means that you can recruit the best candidates for the roles you have to fill.
Decision-making skills: quality inspectors need to consider the benefits and cost implications of standard operating procedures or alterations to evaluation and testing procedures. Their decisions should result in a product that adheres to customer specifications and safety requirements.
Error checking: Identifying any errors or discrepancies in given information ensures that quality inspectors can intervene in the manufacturing process to maintain the quality of products.
Microsoft Office Suite: using Microsoft Office applications in their role means that quality inspectors can evaluate, analyze, and document any updates to standard operating procedures. They must write reports with updates for regulators, internal teams, or management.
Attention to detail: strong attention to detail is an essential skill required by all quality inspectors. They must carefully monitor the production process, identifying any areas that do not meet the requirements and suggesting improvements within guidelines.
Reading comprehension: understanding the information presented in written format to suggest improvements or corrective action is a vital skill required by all quality inspectors if they are to carry out their role effectively.
Useful abilities for a quality inspector
The technical abilities and aptitudes required for quality inspectors allow them to perform their duties ensuring the highest standard of the manufacturing process.
Inductive reasoning: quality inspectors must demonstrate the ability to review pieces of information and find relationships in data to inform the next step when solving a problem.
Oral comprehension: understanding written information and interpreting the key messages enables quality inspectors to write standard operating procedures for others and communicate errors or updates to regulators.
Logical thinking: quality inspectors need to use their logical thinking to solve problems. They must be able to review data and infer the link between data to decide on the best course of action in a given situation.
Problem-solving: a key part of the role of a quality inspector is to troubleshoot any problems that arise and, in some cases, spot issues before they happen. They need to be able to evaluate the available options to select the best course of action.
Teamwork: working as part of a team, quality inspectors need to be able to work and communicate with everyone involved in the manufacturing process. They must deal with conflict situations and ensure the productivity of a team isn't affected by any recommendations they make.
Which soft skills tests could I use to hire a quality inspector?
To determine whether individuals have the soft skills required for the role of a quality inspector, there are several tests that you can include as part of your recruitment process.
Teamwork: a test designed to identify whether candidates can work with others as part of a team. This scenario-based test demonstrates a candidate's ability to trust and effectively communicate with others to achieve a common goal.
Problem-solving: this test assesses individuals' ability to work under pressure and solve problems. Candidates need to use their critical thinking and adaptability skills to determine the best outcome.
Decision-making: in this assessment, candidates are evaluated on their decision-making skills while using their logical thinking and critical reasoning skills. The test is made of situational questions; candidates are required to come to what they believe is the best decision based on the information they have been provided.
Which technical or aptitude tests could I use to hire a quality inspector?
There are several technical and aptitude tests that you can use to ensure that you hire only the candidates with the relevant abilities needed for the job.
Error checking test: this test assesses candidates’ accuracy and attention to detail. It uses different types of information, from verbal to numerical. Candidates need to identify discrepancies in sets of data or texts and select the correct answer.
Microsoft Excel test: a test that requires individuals to use their working knowledge of Microsoft Excel as aligned to the tasks they will encounter in their role.
Numerical reasoning test: this test assesses individuals' aptitude to work with numerical data. They need to use their understanding and practical knowledge of mathematical principles such as percentages, ratios, and fractions to select the correct answer. This test also measures their ability to work under pressure.
Abstract reasoning test: an assessment that evaluates a candidate's ability to think fluidly and laterally, using their logic to solve problems. Individuals need to review sets of patterns or shapes to determine the link between these data sets, then use this information to predict which shape would follow next in the pattern.
Logical reasoning test: a test that uses non-verbal information, where individuals need to use their critical thinking and analytical skills to solve problems. Questions are presented in the form of symbols or images. Candidates need to identify their pattern to choose the correct answer.
Our recommended test battery for a quality inspector
To ensure you recruit suitable candidates for your quality inspector vacancies, we recommend using the following tests in your recruitment process.
Teamwork test: enables you to better understand how well candidates work in a team and whether they can work effectively with others and collaborate to ensure a productive working environment.
Microsoft Excel test: a test that determines an individual's proficiency in using Microsoft Excel and its associated functions to efficiently perform their job as a quality inspector.
Logical reasoning test: demonstrates if candidates can use their logical reasoning and analytical skills to efficiently solve problems.
Numerical reasoning: a test that determines whether candidates are comfortable working with numerical data to solve numerical problems. This test also provides information on their ability to keep calm in stressful situations.
Error checking test: enables you to determine whether candidates can spot inaccuracies in data, procedures, or processes. It also measures their attention to detail while working under pressure to make the correct decisions.
For more information on hiring a quality inspector, check out Neuroworx's page on quality inspector tests.
Boost your hiring power.
Start using Neuroworx today.
Talk is cheap. We offer a 14-day free trial so you can see our platform for yourselves.
Try for free